Cushioned Hydraulic Cylinders
Energy Manufacturing Company designs and manufactures custom hydraulic cylinder cushions. These components are mechanisms designed to gradually decelerate the piston near the end of its stroke to reduce impact forces, minimize shock loads, and prevent damage to the cylinder and connected components.
Fixed cushioning is built into the hydraulic cylinder and has a non-adjustable cushion, making it ideal for applications with predictable loads and speeds.
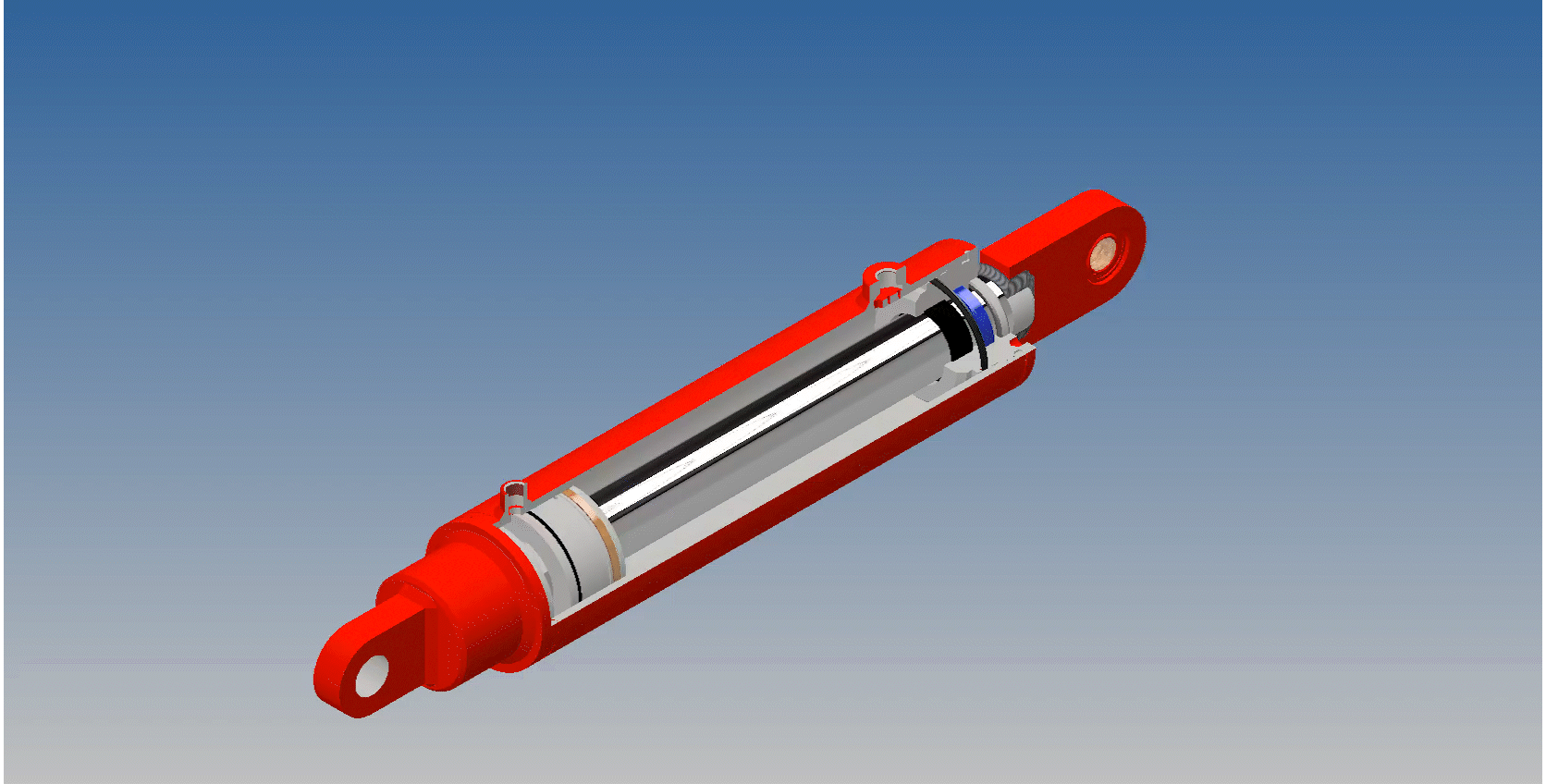
Markets include:
- Aerospace & Defense
- Automation
- Construction
- Industrial
Applications include:
- Earth Moving Machinery
- Landing Gear
- Material Handling Equipment

Smooth Operation

Decelerated Travel
General Features & Specifications
Cushions in Hydraulic cylinder are placed on the end of the piston. A controlled restriction of hydraulic fluid flow creates a damping effect, which gradually slows down the piston before it reaches the end of its cycle. The cushioning mechanism can have one of these features:
- Plunger or Spear. A tapered or stepped projection on the piston rod or end cap that enters a small chamber, reducing the outflow of hydraulic fluid and increasing resistance.
- Metering or Cushioning Orifice. A small hole or adjustable valve controls the rate at which trapped fluid escapes, allowing for fine-tuned deceleration.
- Check Valve (Bypass Valve). Ensures unrestricted fluid flow when the piston moves in the opposite direction, avoiding cushioning on return strokes.
Custom Cushioned Hydraulic Cylinders
At Energy Manufacturing Co., all our cylinders are custom designed. Features that can be tailored to your specific requirements include:
- Size & Shape of Bleed Orifice
- Needle or Valve to Control Fluid Flow
- Cushion Sleeve/Plunger Design
- Cylinder Bore and Rod Size
- Material and Surface Coatings
- Mountings
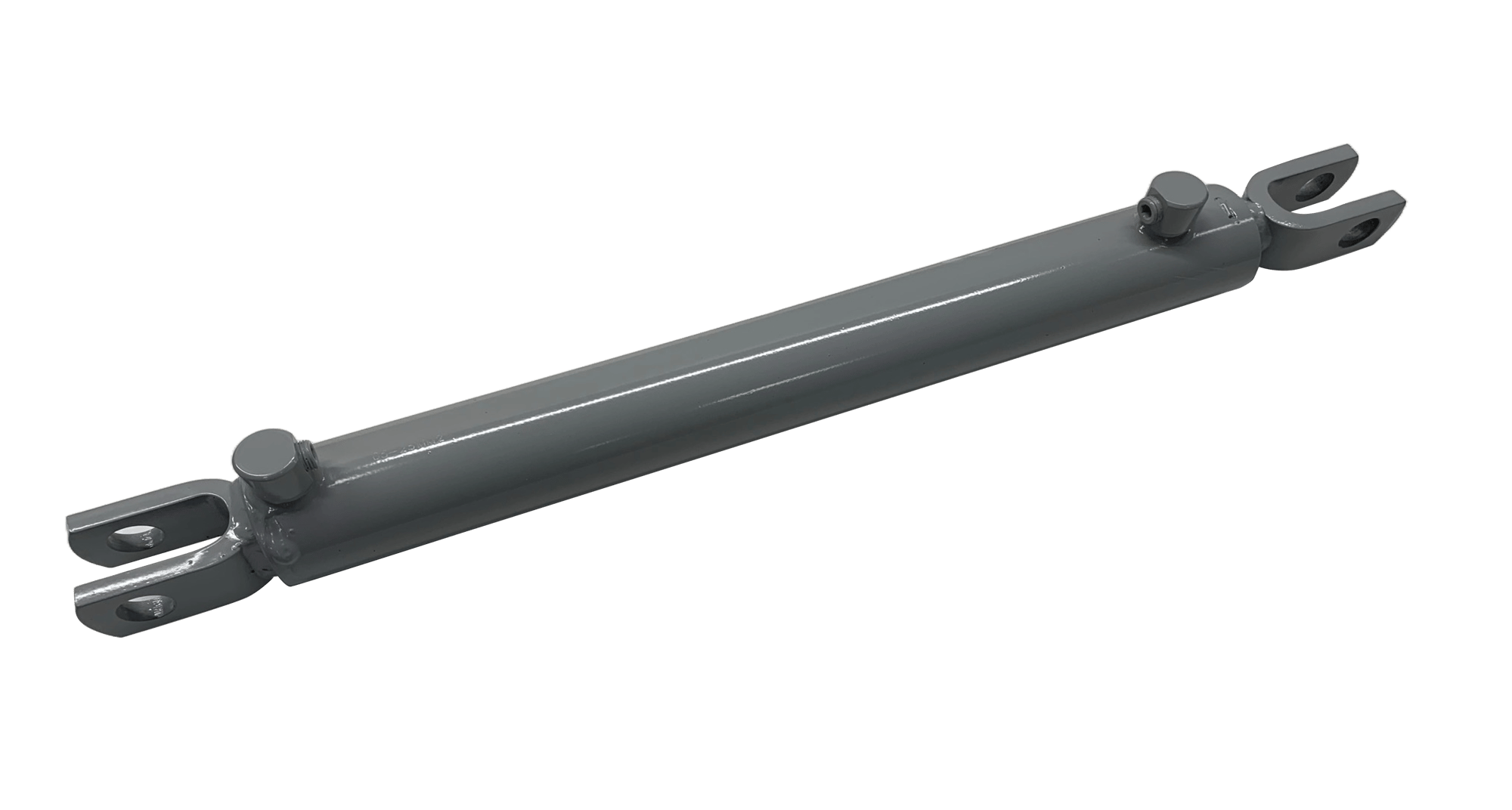
Frequently Asked Questions
Have a question about Hydraulic Cylinder Cushions? We are here to help
What is a hydraulic cylinder cushion, and why is it important?
A hydraulic cylinder cushion is a mechanism integrated into the cylinder that slows down the piston’s movement at the end of its stroke. This controlled deceleration prevents sudden stops and reduces shock, vibration, and noise. It also helps protect the cylinder, machine components, and the entire hydraulic system from premature wear, ultimately extending equipment life and improving operational efficiency.
What types of hydraulic cylinder cushions are available?
-
- Fixed cushions: These are non-adjustable and provide a set level of deceleration. They are simple, cost-effective, and best for applications with consistent load conditions.
- Adjustable cushions allow users to fine-tune the damping effect to match specific operational requirements. They are ideal for varying loads or applications needing precise control. Cushion designs may also vary, such as tapered or orifice-based designs, each offering different damping characteristics.
How do I determine the right cushion size for my hydraulic cylinder?
-
- Bore size. The diameter of the cylinder bore affects the cushion’s effectiveness. Larger bores typically require more robust cushioning.
- Rod diameter and stroke length. These impact the piston speed and force, influencing the cushion requirements.
- Operating pressure and speed. Higher speeds or pressures demand more effective cushioning to manage the increased kinetic energy.
It’s essential to consult with manufacturers or reference technical specifications for accurate sizing.
What materials are used in cushioned hydraulic cylinders, and how do they affect performance?
-
- Polyurethane or rubber. Offers good flexibility and shock absorption. Best for light to moderate loads.
- Metal components (e.g., bronze, steel). Used in high-pressure, heavy-duty applications where durability is critical.
- Composite materials. For applications requiring a balance between strength and flexibility.
The choice of material affects wear resistance, temperature tolerance, and compatibility with hydraulic fluids.
What are the key specifications to consider when selecting a cushioned hydraulic cylinder?
- Pressure rating. Ensure the cushion can handle your system's maximum pressure.
- Operating speed. High-speed applications require cushions designed to manage rapid deceleration.
- Temperature range. Consider the operating environment, as extreme temperatures can affect cushion performance.
- Mounting style and compatibility. The cushion must fit the cylinder design and mounting configuration.
- Fluid compatibility. Ensure the cushion materials are compatible with the hydraulic fluid in use.
Can cushioned hydraulic cylinders be customized for specific applications?
-
- Tailored cushion lengths or damping profiles for unique deceleration needs.
- Material modifications to suit specific environments, like extreme heat or corrosive conditions.
- Special seals or coatings for enhanced durability.
Customization ensures optimal performance but may affect lead times and costs.
What industries commonly use cushioned hydraulic cylinders?
-
- Construction equipment. Excavators, loaders, and cranes rely on cushions for smooth operation.
- Manufacturing and automation. Ensures precision in processes like stamping, pressing, or material handling.
- Agriculture. Tractors and harvesters benefit from reduced shock loads.
- Automotive. Used in vehicle lifts, assembly lines, and testing equipment.
- Aerospace & Defense. Cushioning helps manage forces in harsh environments and precision applications.
How does the cushion design affect the performance of the hydraulic system?
-
- Tapered cushions offer gradual deceleration, ideal for applications needing smooth stops.
- Orifice-based cushions control fluid flow at the end of the stroke, offering more abrupt deceleration.
Poor cushion design or selection can lead to shock loads, system inefficiencies, or even damage to the cylinder or machine structure.
Are there any compatibility issues with existing hydraulic systems?
-
- Mounting configurations. Ensure the cushion matches the cylinder's mount style (e.g., flange, clevis, trunnion).
- Seal materials. Verify that cushion seals are compatible with your hydraulic fluid and temperature conditions.
- System pressure and flow rates. The cushion must accommodate the system's performance characteristics without causing excessive backpressure.
What maintenance is required for cushioned hydraulic cylinders?
-
- Routine inspections. Check for wear, leaks, or degradation of cushion materials.
- Fluid cleanliness. Contaminated hydraulic fluid can cause premature cushion wear.
- Seal checks. Inspect seals for signs of leakage or cracking.
Maintenance intervals depend on the operating conditions and frequency of use.
What are common signs that a cushioned hydraulic cylinder needs to be replaced?
-
- Increased noise or vibration at the end of the stroke.
- Uneven or jerky movements during deceleration.
- Fluid leaks around the cushion area.
- Excessive wear or visible damage to cushion components.
Ignoring these signs can lead to system damage or reduced efficiency.
What is the typical lifespan of a cushioned hydraulic cylinder?
-
- Light-duty applications may see cushions last several years.
- Heavy-duty or high-speed applications might require more frequent replacements.
Regular maintenance and using high-quality materials can extend lifespan.
Contact Us
To learn more about how our innovative cushioned hydraulic cylinders are made to deliver outstanding performance in a range of environments, tell us who you are and briefly describe your application.
When you use Energy Manufacturing Co.’s field-proven hydraulic cylinders with cushioning, you’re getting products that are reliable, rugged, and high-performance.
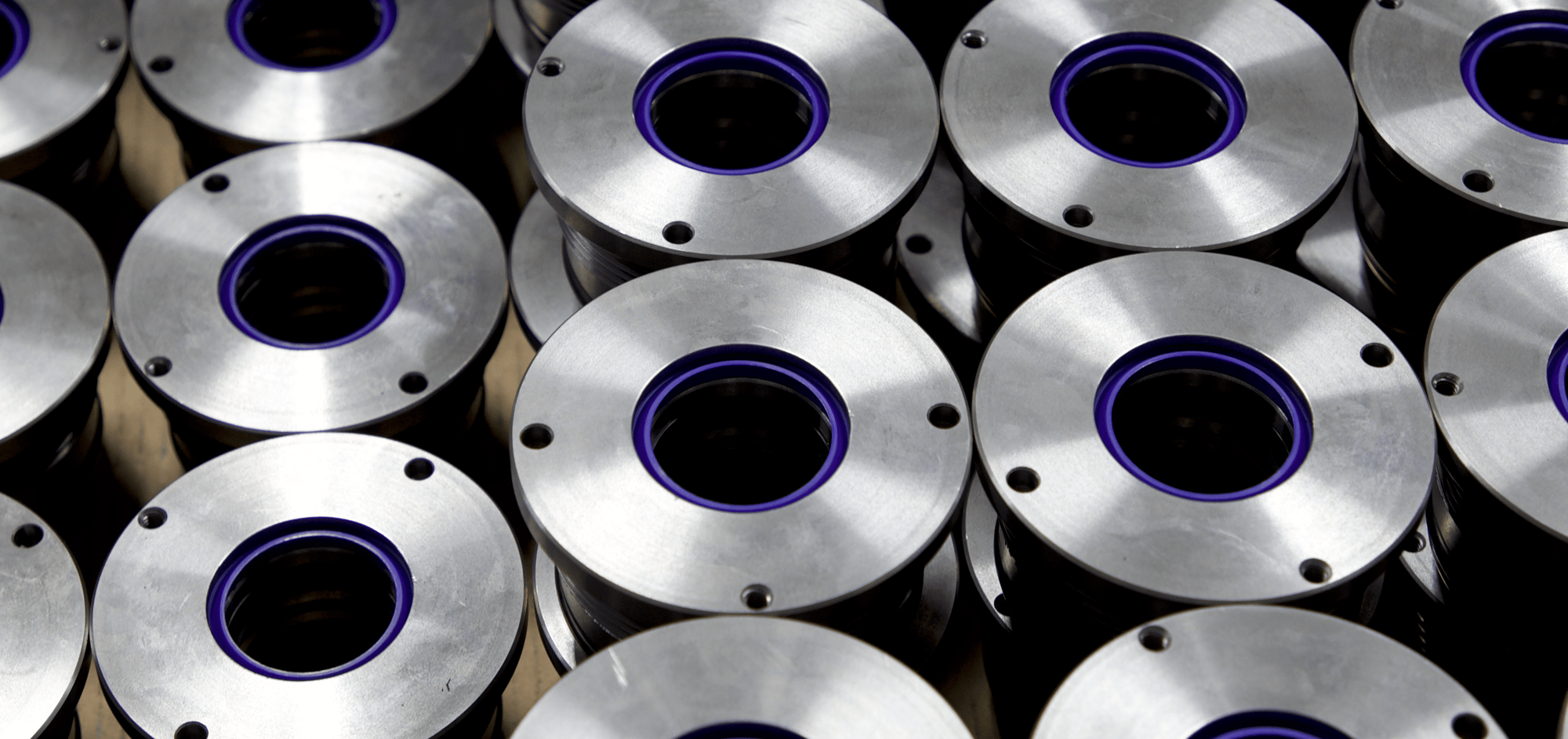